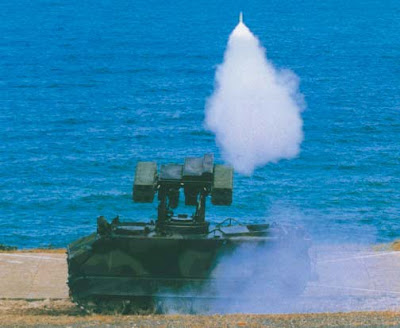
Able to fire up to eight Stinger missiles – each traveling
at Mach 2.2 – the Turkish Armed Forces Pedestal
Mounted Air Defense System (PMADS) delivers
supersonic short-range air defense capabilities for
troops in exposed positions.
Its tactical importance on the battlefield is, however,
only matched by its strategic importance to Turkey’s
national defense industry. After years of manufacturing
defense systems under license, the PMADS program is
the first to be placed with a Turkish company taking the
lead as prime contractor.
As that prime contractor, Aselsan Electronic Industry Inc.
has created an advanced vehicle mounted stinger
platform that delivers significant advantages over the
previous ManPortable Air Defense System (MANPADS)
used by the Turkish Army. In doing so, the company
turned to Radstone Technology to provide the Fire
Control System that lies at the heart of the program.
Faced with the need to deliver uncompromising quality
and reliability as cost-effectively as possible, Radstone
has combined its advanced systems-level expertise with
innovative techniques it has been developing to reduce
costs, weight and production lead times by 30 percent.
“Radstone’s people are very professional,” explains
Mustafa Kaval, Aselsan’s Project Manager for the PMADS
program. “They are technically excellent and have been
very supportive, giving good answers to any questions.
Not only was this our largest-ever weapons systems
integration program, it was our first using COTS. We
needed technology and we needed support that we could
rely on – and Radstone have delivered both.”
Strategic Procurement Policy
The responsibility for coordinating Turkey's large scale
and foreign defense industry and procurement process
lies with the country’s Under Secretariat for Defense
Industries (SSM), an autonomous agency created in 1985
within the Defense Ministry.
In 1997, while announcing that Turkey's annual defense
spending was set to rise steadily to reach a total of $31
billion during the next ten years and as much as $150
billion through to 2025, SSM explained that the spending
would be accompanied by an increasingly stringent
policy of local production to meet the country's defense
procurement needs.
“We have used the last ten to twelve years to establish
our productive defense infrastructure in Turkey. We are
now ready to tackle design and integration capabilities –
goals which the Turkish armed forces fully support,” said
Veysel Yayan, Deputy Under Secretary at SSM at the
time.
The first program to benefit from this strategy
was PMADS. For some years Turkey had
procured a MANPADS version of the
Stinger missile as part of an international
consortium with the Netherlands,
Germany, and Greece. Within that program,
Aselsan produced an electronic guidance
section of the Stinger missile.
Aselsan – A Leading Electronics
Company
Aselsan was founded in 1975 by the Turkish Armed
Forces Foundation to produce tactical military radios and
defense electronic systems for the Turkish Army. Today
Aselsan is the country’s leading multi-product electronics
company, designing, developing and manufacturing
modern electronic systems for military and professional
customers.
Headquartered in Ankara, the company operates through
three main divisions. They are
Communications, covering military and professional
communications systems
• Guidance and Electro-Optics, which manufactures
hybrid microelectronic circuits, night vision
equipment, thermal cameras, laser ranger/designators
and inertial navigation systems
• Microwave and System Technologies, which is
primarily focused on radar, electronic warfare and
command-control systems.
In 1992 SSM commissioned Aselsan to undertake a
feasibility study on the design and production of a
pedestal mounted platform for Stinger missiles which
could be used on two different vehicle platforms.
The ZIPKIN would be based on a fourwheel
Land Rover Defender, while
the ATILGAN would be based on an
armored/tracked M113A2 personnel
carrier.
Aselsan was already very familiar
with the program having started
conceptual studies in 1989 to help
define requirements and how best to
meet them. Kaval, who works in
the Microwave and System
Technologies Division, explains
the drivers for the program. “The
key objectives were to overcome
the limitations of MANPADS,
primarily the fact that the manoperated
system can only fire one missile at
a time and its accuracy is dependent on the skill of
the operator. Our brief was to create an easy to deploy
and fast moving platform that could fire multiple missiles
and be integrated into a single command control system.”
Radstone Provides Development
Platform
PMADS comprises a number of advanced subsystems,
from thermal imaging to a laser rangefinder and the Fire
Control System. “The Fire Control System is actually the
heart of the entire platform,” explains Kaval. “At that time
our systems design experience had been focused
primarily on applications running on PCs. This was to be
our first rugged project and we wanted a vendor that
could not only provide a complete solution for the FCS,
but one that could support us through the development.”
After an exhaustive study, Aselsan concluded that
Radstone was the only company with the board level and
system level expertise required to partner them through
the development program. As the world’s leading
independent supplier of rugged, high-performance COTS
embedded computer products, subsystems and support
software for defense and aerospace applications,
Radstone’s portfolio extends from systems chassis to
boards and completely integrated systems.
But it wasn’t just the technology that attracted Aselsan.
“Radstone offered a very competitively priced solution,
but for me what was even more important was the
support that they showed. They were willing to work
directly with us, without an agent, and even in those
early stages they proved that they could work well with
our engineers.”
The contract was
placed with Radstone
in 1996 to supply a fully
integrated system for the FCS.
It proved to be a sound decision,
especially as Aselsan had only two
and a half years in which to complete
the entire design and development phase, culminating in
a firing range field test.
“It was a very challenging timescale,” recalls Kaval,
“because we not only had to design and integrate all the
subsystems, we also needed to select the best vendors
and complete negotiations with them for each of the
subsystems as well as integrating them into the overall
PMADS system.”
To ease development times, Radstone provided Aselsan
with commercial versions of the boards that would
comprise the final rugged system. Asked how important
those boards were, Kaval is unhesitating. “They were
very, very important. Without that commercial platform
we would not have been able to start our software
development. As soon as we received the platform we
were able to start work on writing our software which
enabled us to shorten the development process by about
six months, so it was critical.”
The completion of the development phase was a series of
demanding firing range tests with the system firing –
while stationary and on the move – targets comprising
metal plates set up on distant hillsides and in-flight
drones. Aselsan and senior observers from the Turkish
Army and SSM were delighted to witness 100 percent
success in all nine test firings.
With this success came the formal completion of the
development phase and negotiations began between
Aselsan and SSM on the exact number of systems
required and other details. “We signed the production
contract in November 2001,” recalls Kaval, “and
Radstone was the first supplier we started to talk to about
the production system.”
Significant Advances in Production
System
With over 40 years serving the military marketplace,
Radstone understands better than most the challenges
posed by the use of COTS components in military
systems destined not only to operate in hostile
environments, but in programs with lifespan stretching up
to 25 years.
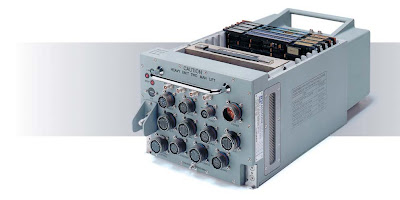
The company’s response has been to develop its concept
of Whole Program Life COTS™ which aims to reduce
overall cost of ownership and provide industry-leading
safeguards against obsolescence. It does so by addressing
the issue at all stages of the program lifecycle, from
designed-in compatibility across generations of products
through to a highly resourced team of design engineers
and support staff dedicated solely to supporting programs
throughout their extended lives.
Part of this approach is a strict policy of maintaining the
‘form, fit, and function’ of boards across generations of
silicon to provide ‘plug and play’ processor upgrades.
While the development system used its PowerPC2A
Single Board Computer (SBC), for the production system
Radstone was able to recommend an immediate upgrade
to the latest generation PowerPC4A.
“I very much agree with Radstone’s policy of maintaining
form, fit and function,” observes Kaval. “Radstone are
leaders in guarding against obsolescence and while we
did not need the performance gains the new processor
offered, it is a very useful means of combating
component obsolescence.”
Radstone’s innovation didn’t stop with a processor
upgrade, however, as the company’s designers worked
with their counterparts in Aselsan to introduce to the
system a range of techniques that Radstone had been
working on.
New Chassis Construction
Among the first improvements was the use of a new
chassis construction method. Previously, Radstone used a
dip brazing process to solder the aluminum walls of a
chassis together to create a very strong enclosure.
However, this method requires the various parts to be
assembled on a jig and moved to a brazing oven where
the temperature needed approaches the melting point of
aluminum. The unavoidable distortion that frequently
results from this method therefore required a postbonding
machining operation.
Transferring lessons learned from another program it had
worked on, Radstone has developed a new way of
bonding the chassis using high performance bonding
agents first developed and used in the aviation industry.
The new technique delivers a chassis with the same
mechanical, environmental and EMC performance as the
dip-brazing method, but in a far more controlled
production process without the need for post-brazing
machining.
Customized Power – off-the-shelf
The power supply for any integrated system typically
represents some 30 percent of total system cost. Radstone
offers a range of power supplies meeting MIL-STD-704E.
However, the vehicle generator environment of the
PMADS meant that Aselsan required a power supply that
met MIL-STD-1275B, where the low voltage operating
level is lower and the spikes and transients are much
more severe – +/-250volt 100micro sec spikes and
100volt 50msec transients.
To meet this requirement Radstone took advantage of a
new approach to power supplies it was developing. The
objective was to break away from the traditional ‘fixed
configuration’ model and derive a cost effective way of
offering flexibility in terms of both Power Supply Unit
(PSU) input specification and output voltage rail
configuration.
To achieve this, Radstone has developed an innovative
approach to power supplies by specifying and then
sourcing a range of power modules which it can ‘mix
and match’ to create a bespoke design that meets a
customer’s precise needs. This means, for example, that if
a customer does not need a particular voltage rail then
they do not have to pay for it merely because it is part of
the ‘standard item’. And in Aselsan’s case, this modular
approach enabled Radstone to design and build a power
supply that met the customer’s particular requirement for
bespoke voltage rail power sequencing and also for the
facility to upgrade in the future to 3.3 volts – something
that would have been impossible in a pre-built
configuration. And because each module is a proven
item, each new power supply configuration carries
inherently less risk than a new design.
Custom 19-layer Backplane and Front
Panel Flex-Circuits
For the development of the prototype system, Radstone
provided an ATR chassis with VMEbus tracking and
wirewrap spills on user-defined pins. These pins can be
wired to a series of connectors and then cabled to the
chassis’ front panel connectors.
In designing the production system, however, Radstone
implemented other innovative techniques, drawing on its
experience and expertise in designing PCBs that use
some of the world’s most advanced construction
materials and practices, combined with an imaginative
approach to wiring to the front panel.
Essentially the two developments are:
• the integration of all I/O wiring into the tracking of the
backplane itself as opposed to wire-wrap
• ‘translating’ the complex cable harnesses from the
backplane to the front panel into easy-to-assemble
flexible interconnects known as flex-circuits.
To achieve tracking in the backplane itself, Radstone
added seven additional electrical tracking layers to a
standard PCB backplane which comprises 12 layers.
Conventional approaches carrying these signals as a
mesh of complex cables, each configured to reflect the
nature of the signal – in terms of, for example, a twisted
pair compared to a screen twisted pair – and which cater
for specific interfaces which might have controlled
impedances.
Typically, the time taken to manually wire a chassis took
six weeks – Radstone’s new approach slashed that time
down to two days.
Using advanced CAD tools, Radstone’s engineers
recreated the wiring as circuits which were translated
within the seven tracking layers of the backplane. The
characteristics of the different cable types were reflected
in the design. For example, twisted pair cable was
simulated by parallel traces, and screening by guard
traces, connected to digital ground above and below the
signals.
For the connection from the backplane to the front panel
Radstone again offered an innovative solution through the
use of flexible circuits which could be easily attached to
either end of the PCB.
“But while the use of flex-circuits has saved a lot of
time,” observes Kaval, “the most important thing for me is
that it reduces the risk of wrongly routed circuits or short
circuits. Translating most of the wiring into the tracking
dramatically reduces any scope for human error, as well
as streamlining the assembly process.”
Future developments have again been designed-in, with
the tracking for a 1553 interface already included which
will enable PMADS to interface to digital launchers when
required.
Completing this part of the system is the chassis’ front
panel, for which a bespoke configuration of connectors
was designed to meet Aselsan’s particular needs which
included the use of gaskets in case the chassis is subject
to ‘hose down’ in the field.
Radstone’s attention to detail went as far as ensuring that
there was sufficient space around connectors to enable
easy connections by gloved hands.
Thermal Analysis and System Testing
Radstone’s approach to thermal management starts with
component selection and placing. Critically, the company
designs its own boards which represent the leading edge
of PCB technology with micro-vias, laser imaging and
new laminate materials harnessed to improve thermal
conductivity and provide enhanced stiffness to reduce the
harmful effects of vibration. But while Aselsan’s system
benefits from being air-cooled via an avionics-class fan
drawing air over the surface of the boards and out of the
chassis, leaving nothing to chance Radstone undertook a
full thermal analysis using Flomerics’ FLOTHERM.
As board level configurations were defined, Radstone
performed a full system level thermal analysis to validate
that, in theory at least, using standard Level 4 boards (-40
deg C to +75 deg C) would meet the required operating
temperature range for the equipment. This theoretical analysis was later backed up by measurements made on individual production
units, including putting the entire production system successfully through full
type approval testing, including full Environmental Stress Screen (ESS) and
temperature cycling and random vibration testing.
As with all Radstone systems, testing does not end with successful
qualification. For each of its products the company writes a set of test
paradigms that deliver built-in-test (BIT) firmware to assure confidence in the
operation of equipment at power up, and also a BCS (Background Condition
Screening) toolset that goes beyond the field capabilities of BIT to provide
continuous test routines during actual deployment – with no loss of
performance.
The Importance of Teamwork
Kaval’s experience of working with Radstone has been so positive that he has
recommended the company to other parts of Aselsan, and importantly, the
success of PMADS has seen a prototype of a naval variant – the BORA – enter
field trials.
While Kaval is the first to acknowledge the technical innovation and
leadership Radstone has demonstrated, asked for what he feels has been
Radstone’s most significant contribution his response is ‘teamwork’.
“Radstone’s technology is impressive, but so too are their people. Our
engineers have built up very good working relationships with their engineers
and there have been several visits by each group of engineers to the other.
They are,” Kaval says simply, “compatible.”
J-14 aircraft hi-res images:
ReplyDeletehttp://china-arsenal.blogspot.com/2010/01/j-14-aircraft-hi-res-images.html
This comment has been removed by the author.
ReplyDelete